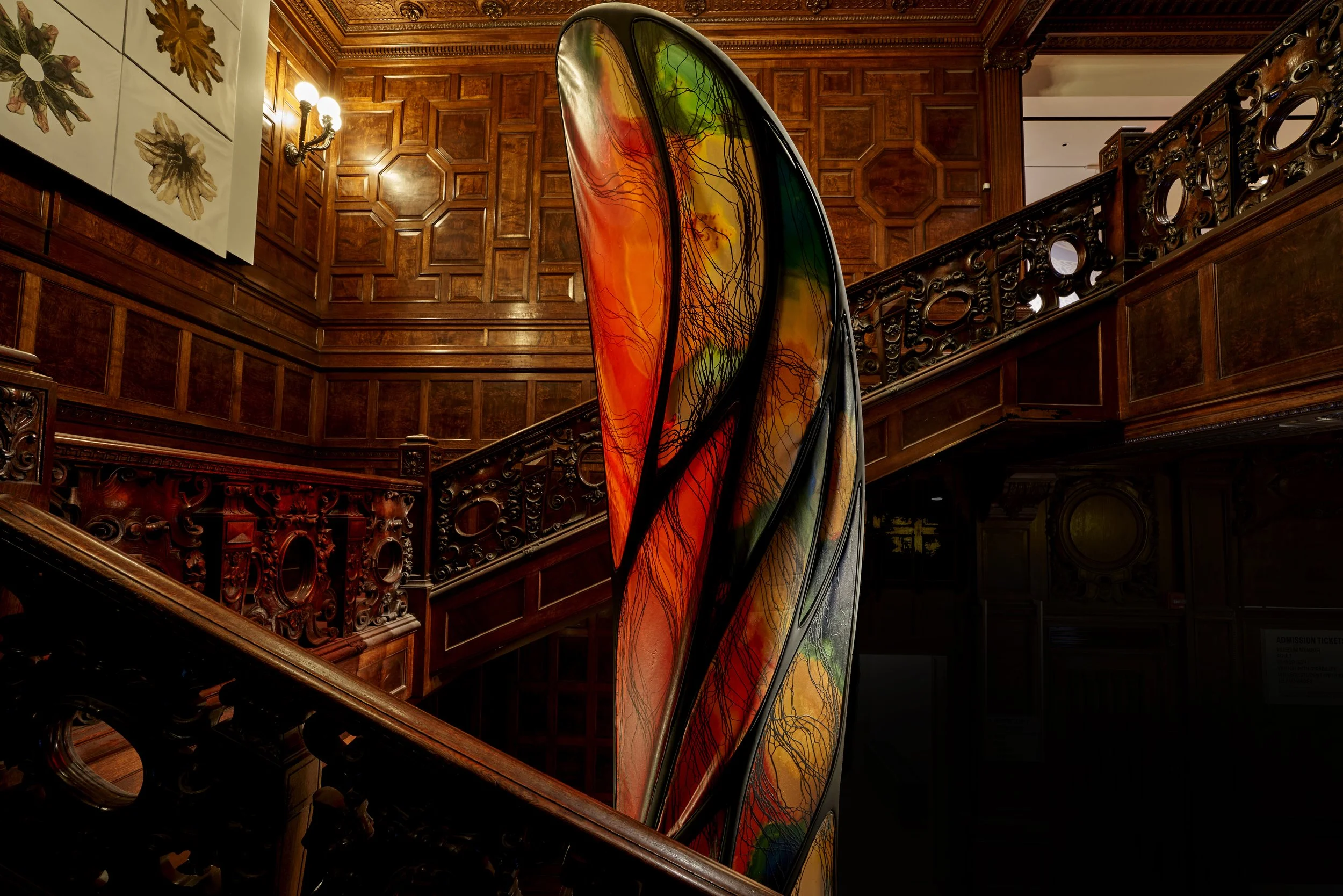
Aguahoja II
Aguahoja II builds upon the platform technology of its predecessor, enabling large-scale multi-material 3D printing with abundant, organic materials.

Motivation
Since the Industrial Revolution, the design of objects and structures has been dominated parts. Within a design, each individual part is typically composed of a single material, such as a metal cog, and provides no function on its own. Natural systems, by contrast, are formed from gradients of material with no clear boundary between individual parts. The trunk of a tree narrows into branches that slowly transition into leaves with subtle gradients of material and form.
The ability to design objects that that contain such gradients of material has only recently become possible through the advent of multi-material 3D printing systems. Aguahoja II builds upon the library of abundant, sustainable composites developed for Aguahoja I with the novel capability to 3D print gradients of multiple materials.
Transitions between strong, rigid sections and soft, flexible occur seamlessly within Aguahoja II’s biopolymer skin. These gradients are made visible through the incorporation of natural pigments and dyes from beetroot, turmeric, butterfly-pea flower, and squid-ink. From these colors, patterns inspired by those used by organisms to communicate with one another are arrayed across the structure’s skin.

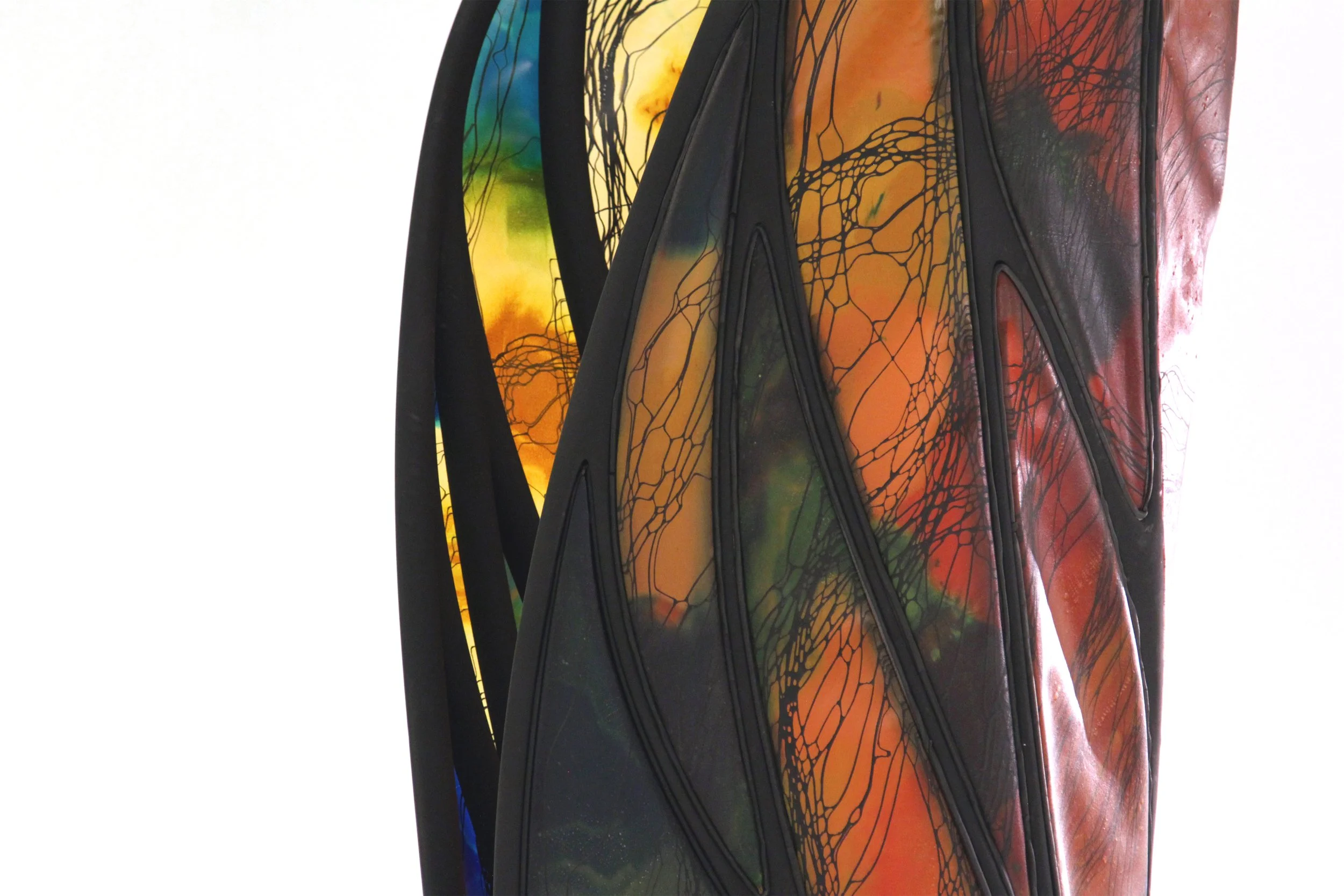
Overview
Aguahoja II was constructed in 2019 for display in the Cooper Hewitt Smithsonian Design Museum’s design Triennial. The structure is second in a series of prototypical towers designed to demonstrate the large-scale 3D printing of organic materials. Each structure is composed of an organic skin bound to a synthetic photopolymer skeleton and stands at 5 meters tall.
The structure’s skin is made from three of nature’s most abundant materials – cellulose, chitin, and pectin. These materials are mixed into hydrogel solutions and 3D printed at room temperature without any synthetic binding agents. By tuning the ratios of each of these components, composites can be printed that are flexible and tough like leather or strong and rigid like wood. Furthermore, just as in nature, these printed composites retain their ability to react to environmental changes in temperature and humidity.
By avoiding the use of synthetic additives and using minimally refined organic matter, the organic composites printed for Aguahoja retain their ability to be decomposed and digested by organisms, transferring the nutrients and energy within them to fuel new growth. In this way, Aguahoja aims to bridge the gap between humans and non-human ecosystems, pointing towards a future where the grown and the made unite.
Digital Fabrication
Aguahoja II’s organic skin is designed through a procedural pipeline that assigns material properties based on input environmental parameters. Structural simulation guides the distribution of strong, rigid materials and soft, pliable materials in regions of high load and high displacement respectively. These materials are then assigned colors based on designed patterns that mirror those used for communication amongst other organisms. The machine code required to print layers of graded material that form these gradients when dried is generated automatically.
To provide additional reinforcement, a generative pattern of rigid veins containing high concentrations of cellulose is distributed within the multi-material skin. These veins are created by an agent-based model that aggregates in areas of high structural stress but disperses in areas of high illumination where the patterns are meant to be most visible. This generative system can be applied to any input geometry, allowing for the rapid generation of a designed structure and the machine code required for its fabrication.
Materials
Typical multi-material printing systems require separate print-heads for each material and complex systems that control the deposition of material. Aguahoja II employs the novel method of Sequential Multi-Material Additive Manufacturing (SMMAM), which allows for the creation of high-resolution material gradients with only a single nozzle. During SMMAM, layers of semi-liquid material are printed into one another with variable pressure. As these layers dry, the printed material locally diffuses to form blended regions. The properties of these blended regions are comparable to mixtures blended prior to printing. SMMAM is described in the United States patent Methods and apparatus for parametric fabrication.
Energy and Ecology
Structures in the Aguahoja series leverage a mix of renewable and non-renewable inputs in a system with feedback flows through the decomposition of structural materials. Organic materials and their refinement account for the system’s largest energetic inputs. Approximately 13% of the system’s energy is drawn from renewable systems, substantially higher than conventional architecture but lower than agricultural systems. Despite the relatively small physical footprint of structures in the Aguahoja series, their material flows are global.
More information in Method
Aguahoja II / 2018
-
Acknowledgements
The Mediated Matter Group
Nic Lee , Joshua Van Zak, Joseph Henry Kennedy, Ramon Elias Weber, Jorge Duro-Royo, Christoph Bader, João Costa, Sunanda Sharma, James Weaver, and Prof. Neri Oxman
Research Collaborators
Joseph Faraguna, Danielle Grey-Stewart, Amelia Wong, Ava Iranmanesh, Prof. Pam Silver
Substructure Production
Stratasys, Ltd., Stratasys Direct Manufacturing
Further Acknowledgements
MIT Media Lab, Oxman LLC, Stratasys Ltd, MIT Research Laboratory of Electronics, Wyss Institute at Harvard, Department of Systems Biology at Harvard, GETTYLAB, Robert Wood Johnson Foundation, Autodesk BUILD Space, TBA-21 Academy, Thyssen-Bornemisza Art Contemporary, Stratasys Direct Manufacturing, National Academy of Sciences, San Francisco Museum of Modern Art, Esquel Group.
-
Publications
Multi-Material Printing of Multi-Lengthscale Bio-composite Membranes. Lee, N., Weber, R. Kennedy, J H., Van Zak, J., Duro-Royo, J., Oxman, N., Proceedings of the IASS Annual Symposium (2019)
Sequential multimaterial additive manufacturing of functionally graded biopolymer composites. Lee, N. A., Weber, R. E., Kennedy, J. H., Van Zak, J. J., Smith, M., Duro-Royo, J., & Oxman, N. (2020). 3D Printing and Additive Manufacturing, 7(5), 205-215.
Patents
Methods and Apparatus for Parametric Fabrication
Joshua Van ZakJorge Duro RoyoAndrea LingYen-Ju Tai, Nicolas Lee, Barrak DarweeshJoseph Henry Kennedy, JR., Neri Oxman
-
Awards and Recognition
Awards
Fastcompany’s Most Innovative Sustainability Projects of 2020, Finalist
Exhibitions
San Francisco Museum of Modern Art, Nature X Humanity, 2022
Cooper Hewitt Smithsonian Design Museum, Triennial, 2019
Cube Design Museum, 2019
Press