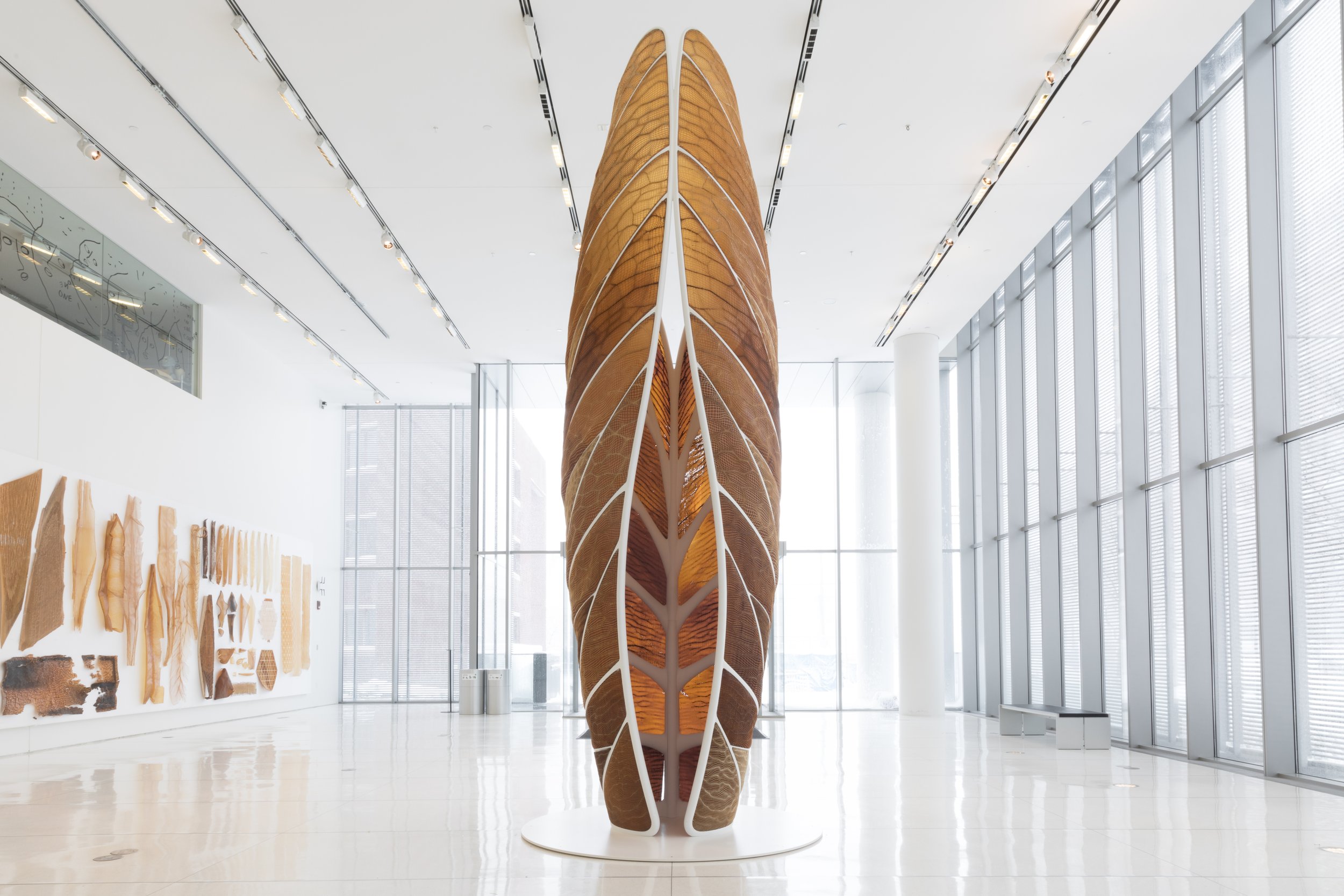
Aguahoja I
Aguahoja is an exploration of Nature’s design space – an effort to build with materials that are grown, live and respond to their environment, and ultimately die to fuel new growth.
Motivation
Nature made us half water. With water, and through growth and degradation, the biological world facilitates customization of an organism’s physical and chemical properties as a function of genes and environmental constraints.
By contrast, the built environment is comprised of artificial, inanimate structures designed to perform a finite set of predefined functions. When their function is served or outlived, they become permanent waste in our landfills and oceans. Upon malfunctioning or degrading, the majority of plastics, woods, glass, and metals are never recycled. Specifically, more than 300 million tons of plastic are produced globally each year, leaving harmful imprints on the environment: our seas, our trees, and our bodies. Less than 10 percent of this material is recycled, and the rest becomes waste, dumped into landfills and oceans. Raw ingredients utilized by these materials are extracted from the earth faster than they can be replenished, and are processed using toxic chemicals that leach out of these goods as they degrade back into the earth over thousands of years.
Derived from organic matter, printed by a robot, and shaped by water, Aguahoja points towards a future where the grown and the built are one in the same. It embodies the Material Ecology design approach to material formation and decay by design, as well as the realization of the ancient biblical verse “from dust to dust”―from water to water.
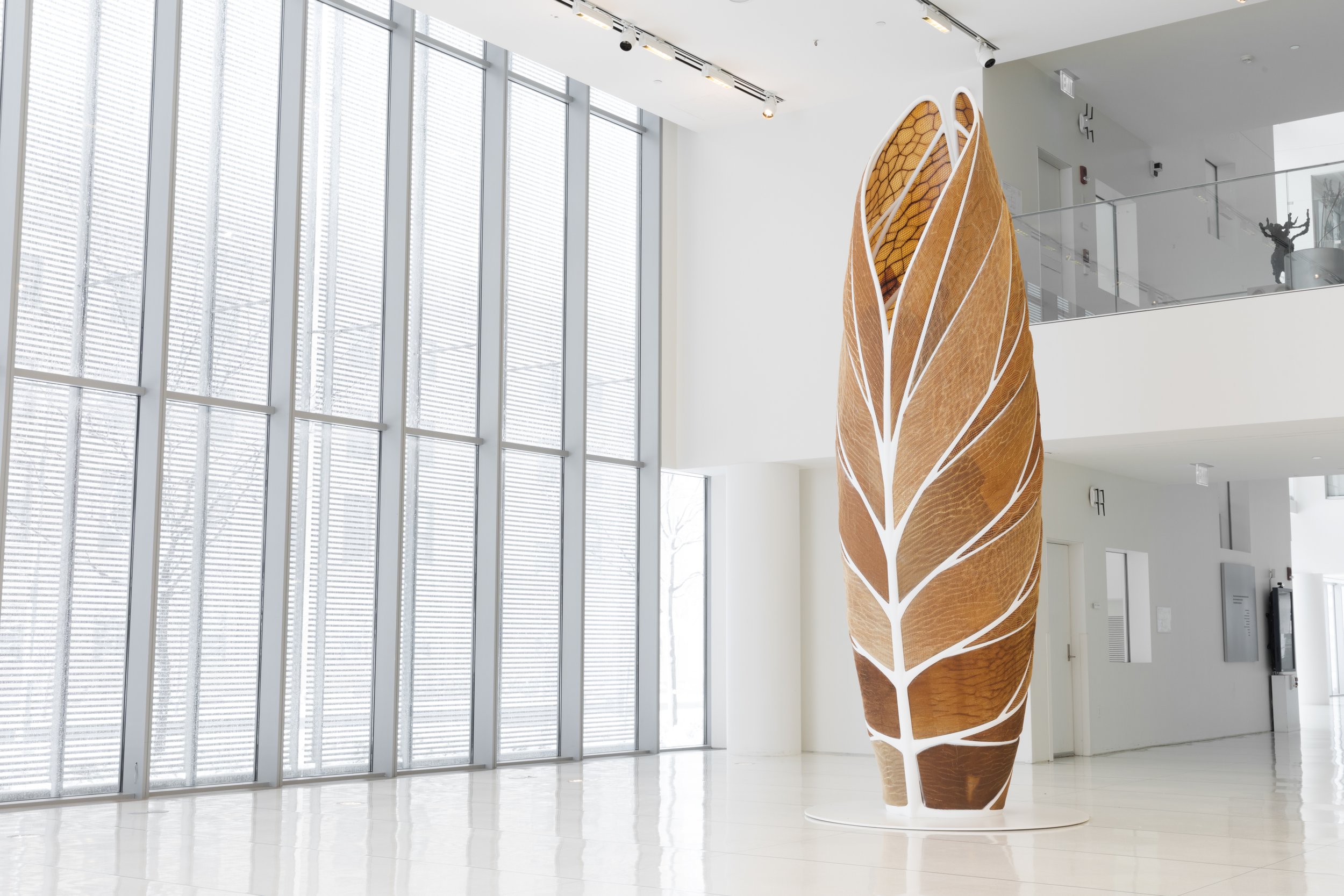
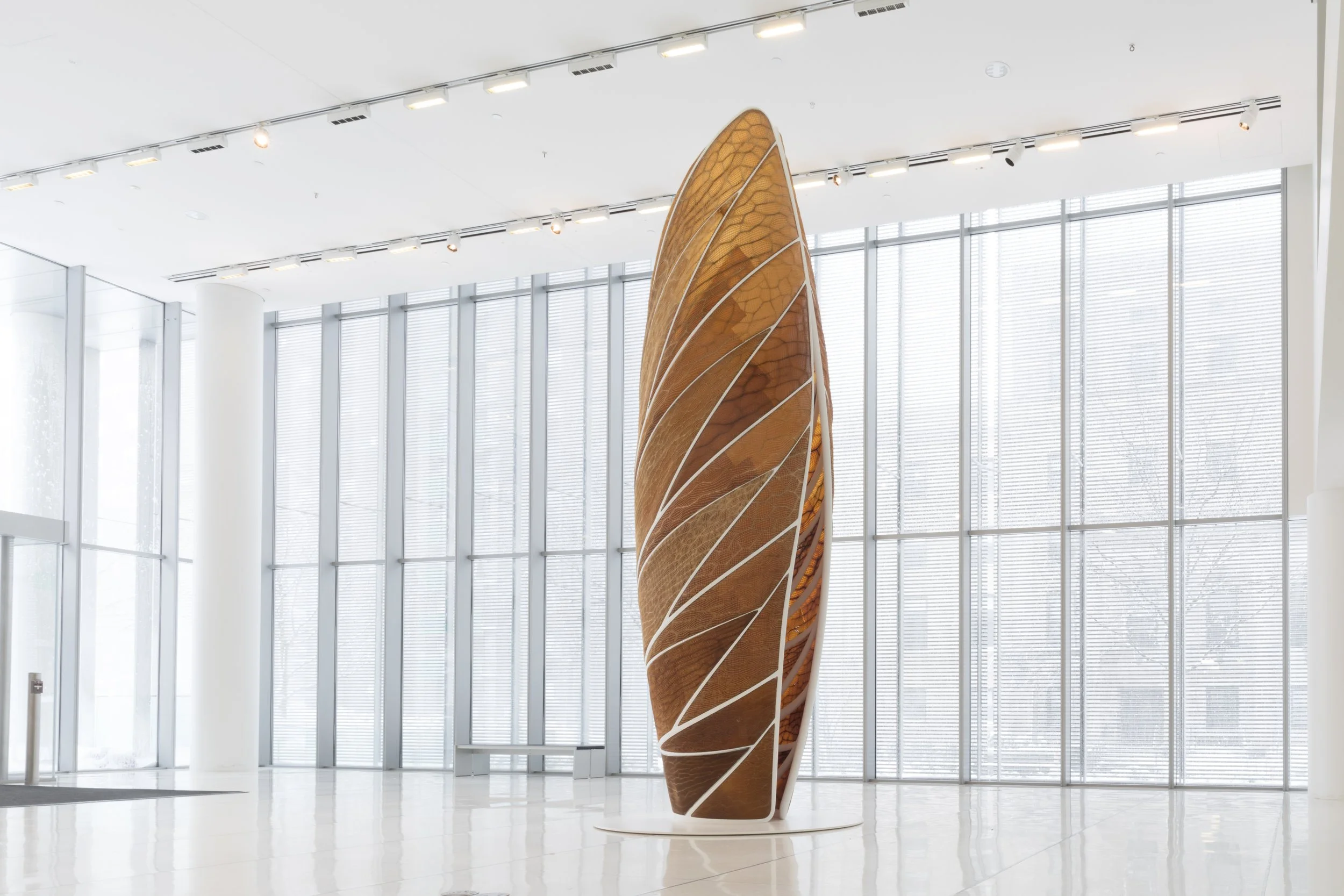
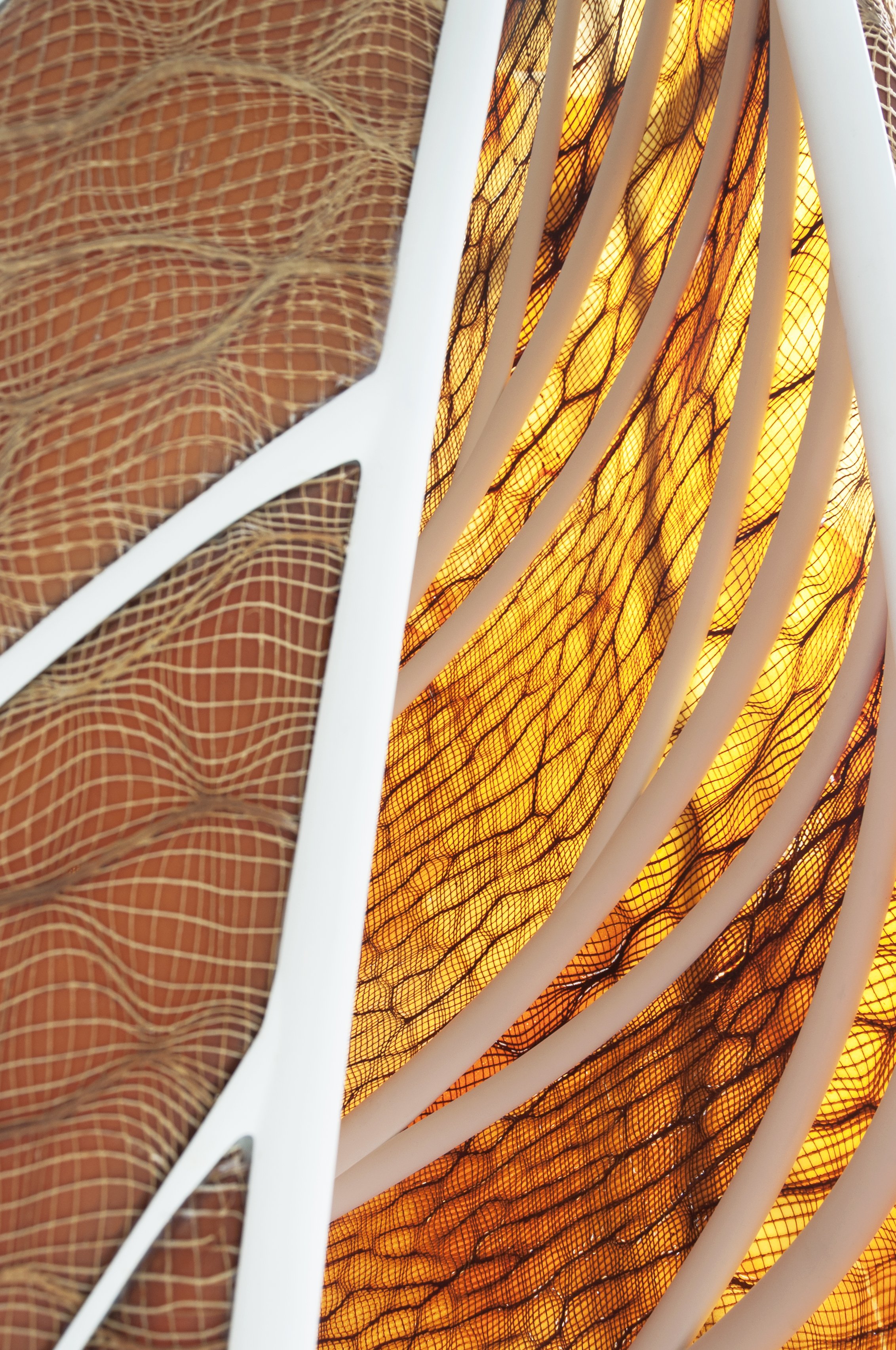

Overview
Aguahoja was constructed in 2017 for display in the MIT Media Lab. It has since been displayed in the Museum of Modern Art, Centre Pompidou, and the San Francisco Museum of Modern Art. The structure is the first in a series of prototypical towers designed to demonstrate the large-scale 3D printing of organic materials. Each structure is composed of an organic skin bound to a synthetic photopolymer skeleton and stands at 5 meters tall.
The structure’s skin is made from three of nature’s most abundant materials – cellulose, chitin, and pectin. These materials are mixed into hydrogel solutions and 3D printed at room temperature without any synthetic binding agents. By tuning the ratios of each of these components, composites can be printed that are flexible and tough like leather or strong and rigid like wood. Furthermore, just as in nature, these printed composites retain their ability to react to environmental changes in temperature and humidity.
By avoiding the use of synthetic additives and using minimally refined organic matter, the organic composites printed for Aguahoja retain their ability to be decomposed and digested by organisms, transferring the nutrients and energy within them to fuel new growth. In this way, Aguahoja aims to bridge the gap between humans and non-human ecosystems, pointing towards a future where the grown and the made unite.
Digital Fabrication
Aguahoja I is designed and fabricated using a novel method of Water-Based Digital Fabrication. This platform technology enables the high-resolution, large-scale 3D printing of organic materials at room temperature without any synthetic binding agents. The shape and material composition of the printed composites are directly informed by physical properties (e.g., stiffness and opacity), environmental conditions (e.g., load, temperature, and relative humidity), and fabrication constraints (e.g., degrees-of-freedom, arm speed, and nozzle pressure), among others. This platform fosters tight integration between form, function, and fabrication at scales that approach and often match the biological world.
The organic materials used in this printing process retain their natural sensitivity to environmental conditions such as temperature and humidity. A composite that is typically strong and rigid may turn temporarily pliable in humid environments. Aguahoja I leverages these interactions as an asset by beginning with the simulation of a structure’s environment and using this data to drive the distribution of materials within a structure. The result is the creation of large-scale, sustainable structures that dynamically live and respond to their environment.
Materials
Aguahoja I establishes a library of 3D printable organic composites formed from the most abundant materials on the planet. Cellulose, collected from lumber waste, adds strength and stiffness to these composites, while chitosan, derived from the chitin waste of the shellfishing industry, serves as a tunable binding agent. Pectin from apple skins can be added to these composites to enhance their flexibility and toughness. As in nature, small variations in the ratios of these materials lead to large changes in mechanical properties, enabling a vast array of material properties from a relatively small pallet of stock components.
Through the use of material models, the mechanical properties resulting from specific combinations of materials can be predicted and leveraged within a design. Aguahoja I uses variations in material composition and geometry in order to reinforce areas of high structural stress and to program the structure’s eventual decomposition when exposed to rainfall. These capabilities make Aguahoja’s material library the step towards materials that do not become waste, but instead live and dynamically react to their environments before ultimately decomposing to fuel new growth.
Energy and Ecology
Structures in the Aguahoja series leverage a mix of renewable and non-renewable inputs in a system with feedback flows through the decomposition of structural materials. Organic materials and their refinement account for the system’s largest energetic inputs. Approximately 13% of the system’s energy is drawn from renewable systems, substantially higher than conventional architecture but lower than agricultural systems. Despite the relatively small physical footprint of structures in the Aguahoja series, their material flows are global.
Aguahoja / 2018
-
Acknowledgements
The Mediated Matter Group
Jorge Duro-Royo, Joshua Van Zak, Yen-Ju (Tim) Tai, Andrea Ling, Nic Lee, Barrak Darweesh, Laia Mogas-Soldevilla, Daniel Lizardo, Christoph Bader, João Costa, Sunanda Sharma, James Weaver, Prof. Neri Oxman.
Research Collaborators
Joseph Faraguna, Matthew Bradford, Loewen Cavill, Emily Ryeom, Aury Hay, Yi Gong, Brian Huang, Tzu-Chieh Tang, Shaymus Hudson, Prof. Pam Silver, Prof. Tim Lu
Substructure Production
Stratasys, Ltd., Stratasys Direct Manufacturing
Music Composition
Jeremy Flower
Video Production
The Mediated Matter Group, Paula Aguilera, Jonathan Williams
Further Acknowledgements
MIT Media Lab, NOE. LLC., Stratasys Ltd., MIT Research Laboratory of Electronics, Wyss Institute at Harvard, Department of Systems Biology at Harvard, GETTYLAB, Robert Wood Johnson Foundation, Autodesk BUILD Space, TBA-21 Academy, Thyssen-Bornemisza Art Contemporary, Stratasys Direct Manufacturing, National Academy of Sciences, San Francisco Museum of Modern Art, Esquel Group
-
Publications
*Designing a Tree: Fabrication Informed Digital Design and Fabrication of Hierarchical Structures
Duro-Royo, J., Van Zak, J., Ling, A., Tai, Y-J., Hogan, N., Darweesh, B., and Oxman, N. (2018),
Proceedings of the IASS Annual Symposium. 2018
*Designing (for) Decay: Parametric Material Distribution for Hierarchical Dissociation of Water-based Biopolymer Composites
Tai, Y-J., Bader, C., Ling, A., Disset, J., Darweesh, B., Duro-Royo, J., Van Zak, J., Hogan, N., and Oxman, N. , (2018), Proceedings, of the IASS Annual Symposium.
*Indicates publication under former name, Nicolas Hogan
-
Awards and Recognition
Awards
Fastcompany’s World Changing Ideas, Winner for Art and Design, 2020
Dezeen Sustainable Design of the Year, 2019
Dezeen Design Project of the Year, 2019
Exhibitions
San Francisco Museum of Modern Art, Nature X Humanity, 2022
Museum of Modern Art, Material Ecology, 2020
Centre Pompidou, Le Fabrique du Vivant, 2019
Press
Aguahoja - Programmable Water-Based Biocomposites, Creative Applications
Neri Oxman and MIT Develop Programmable Biocomposites for Digital Fabrication, Arch Daily